How to prevent bearing failure of DCY200-40-1S hard tooth gear reducer
To prevent the bearing failure of DCY200-40-1S hard tooth gear reducer, measures can be taken from correct selection, installation and commissioning, lubrication maintenance, operation monitoring, etc., as follows:
Correct selection and installation
Reasonable selection: Based on the load characteristics, speed, working environment, and other factors of the DCY200 reducer, select the appropriate type and specification of bearings to ensure that their load-bearing capacity and performance meet the actual working requirements.
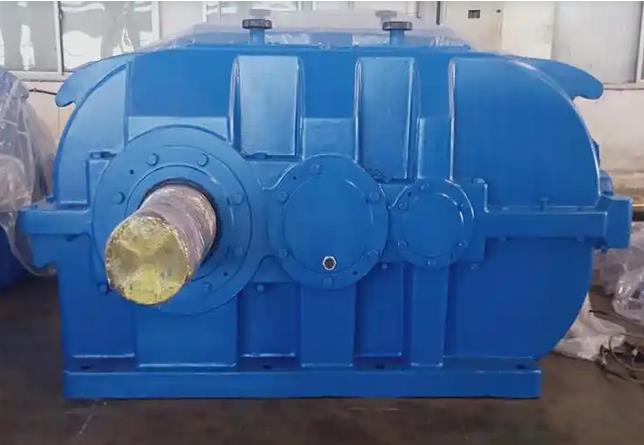
Accurate installation: During installation, strictly follow the installation instructions to ensure the accuracy of the fit between the bearing, shaft, and bearing seat. Use professional installation tools and methods to avoid damage to the shaft. At the same time, it is necessary to ensure that the coaxiality and perpendicularity of the shaft and bearing seat meet the requirements, to prevent the bearing from bearing additional radial or axial forces during operation.
Good lubrication and sealing
Choose the appropriate lubricant: Based on the working conditions of the bearing, choose lubricating oil or grease with good lubrication performance, wear resistance, and oxidation resistance. For DCY200 bearings, medium load industrial gear oil can generally be used, and its viscosity should be reasonably selected based on factors such as operating temperature and speed.
Regular inspection and replacement of lubricants: Establish a regular lubrication system inspection system to ensure that the oil level of the lubricating oil is normal and avoid situations where the oil level is too low, resulting in insufficient lubrication, or too high, resulting in poor heat dissipation. At the same time, replace the lubricating oil according to the prescribed cycle to prevent the lubricating oil from aging, contaminating and losing its lubrication performance.
Ensure good sealing: Use reliable sealing devices such as oil seals, sealing rings, etc. to prevent lubricating oil leakage and external dust, moisture, and other impurities from entering the bearing, thereby avoiding bearing failure caused by poor lubrication or impurities entering.
Strengthen operation monitoring and maintenance
Temperature monitoring: During the operation of the gearbox, the temperature of the bearings is regularly monitored by installing temperature sensors or using infrared thermometers. Once an abnormal increase in bearing temperature is detected, it is necessary to stop the machine for inspection in a timely manner, identify the cause, and take corresponding measures.
Vibration monitoring: Use vibration monitoring instruments to regularly monitor the vibration of bearings. The sudden increase in vibration value is often an early signal of bearing failure. By analyzing the vibration signal, it is possible to determine whether the bearing has problems such as wear and looseness.
Regular inspection: Develop a detailed regular inspection plan to conduct a comprehensive inspection of bearings, including their appearance, clearance, wear, etc. When inspecting, pay attention to observing whether there are signs of damage such as wear, cracks, and peeling on the surface of the bearing, and measure whether the clearance of the bearing is within the specified range.
Avoid overload operation: Strictly operate according to the rated load of the reducer to avoid overload operation. In actual operation, real-time monitoring of the load is necessary to ensure that the load is within the bearing's carrying capacity range.