What impact will bearing damage have on the DCY250-45-1S three-stage gear reducer
In the DCY250-45-1S three-stage gear reducer, bearing damage can have multiple impacts, as follows:
Affects transmission accuracy
Causing poor gear meshing: After the bearing is damaged, the position and rotation accuracy of the shaft will be affected, making it impossible for the gears installed on the shaft to maintain the correct meshing position and clearance. This can lead to problems such as gear misalignment and local wear during transmission, further affecting transmission accuracy and reducing the stability of output speed and torque.
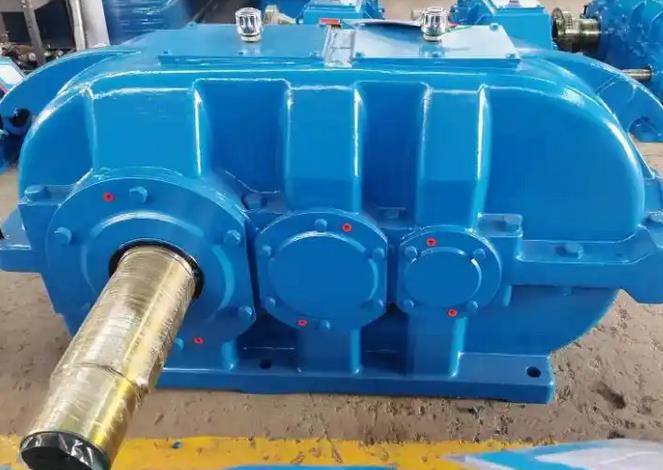
Reduce transmission efficiency
Increased friction and energy loss: Bearing damage will increase the friction between the shaft and the bearing, and at the same time, due to the deterioration of gear meshing, the friction between gears will also increase. These additional frictions will consume more energy, leading to a decrease in the transmission efficiency of the gearbox and requiring more electrical or other power sources to be consumed during equipment operation.
Generate abnormal vibrations and noise
Causing mechanical vibration: Damaged bearings will produce irregular jumping and vibration during operation, which will be transmitted to gears and other components through the shaft, causing vibration of the entire gearbox. Vibration not only affects the stability of equipment, but may also cause loose connecting components, further affecting the normal operation of the equipment.
Noise generation: When a bearing is damaged, abnormal friction and collision will occur between its internal rolling elements and raceways, resulting in noise. At the same time, gears can also produce noise due to poor meshing, and these noises can overlap with each other, causing the gearbox to make obvious abnormal noises during operation, affecting the working environment, and may be a warning signal of equipment failure.
Accelerated component wear
Exacerbating gear wear: Due to bearing damage causing poor gear meshing, the gear tooth surface will bear uneven loads, resulting in increased pressure on local tooth surfaces and accelerating gear wear. The tooth profile of the worn gear will change, further deteriorating the meshing state, forming a vicious cycle, and shortening the service life of the gear.
Impact on shaft wear: After the bearing is damaged, the clearance between the shaft and the bearing increases, causing the shaft to shake and deflect during operation. This will intensify the wear on the joint between the shaft and the bearing, resulting in a decrease in the dimensional accuracy and surface quality of the shaft. In severe cases, the shaft may need to be replaced.
Causing equipment malfunction or even shutdown
Triggering chain reaction: If bearing damage is not detected and dealt with in a timely manner, it may trigger a series of chain reactions, such as gear breakage after severe wear, excessive shaft wear may lead to shaft fracture, etc. These faults will cause the gearbox to malfunction, resulting in equipment shutdown, affecting the production process, and causing economic losses.
Safety hazard: In some cases, gearbox failure may have an impact on the safety of the entire production system. For example, in some large mechanical equipment, a sudden failure of the gearbox may cause the equipment to lose control, leading to safety accidents and endangering the lives of operators and the safe operation of the equipment.