Specific measures to strengthen the quality control of K47-YVP2.2-4P-9.1-M1-270 gear reducer
Strengthening the quality control of K47 reducer can be achieved through measures such as raw material procurement, production process, assembly process, inspection and testing, and after-sales service, as follows:
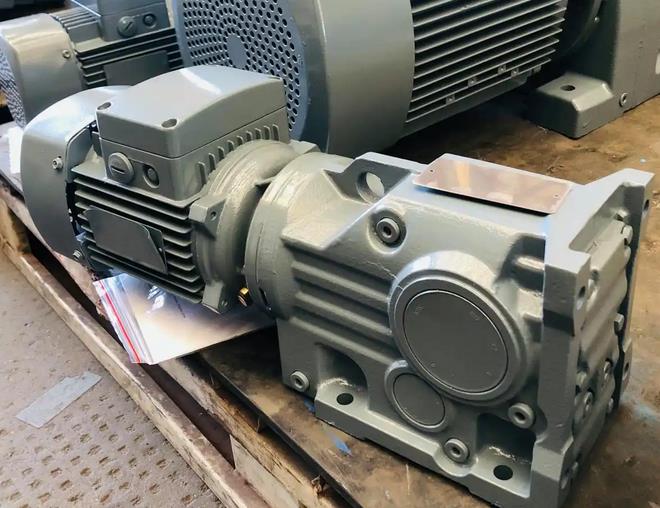
Raw material procurement process
Strict supplier screening: Conduct a comprehensive evaluation of raw material suppliers, including their production capacity, quality control system, industry reputation, etc. Choose suppliers with stable production capacity and good quality reputation to establish long-term cooperative relationships.
Strengthen raw material inspection: Conduct strict inspections on every batch of purchased raw materials, such as steel, cast iron, bearings, oil seals, etc. Check whether the chemical composition, physical properties, dimensional accuracy, etc. of the materials meet the design requirements to ensure the stability of the raw material quality.
process control
Optimize machining process: Based on the structural characteristics and precision requirements of K47 reducer, develop a reasonable machining process route. Optimize the process for key processes such as gear machining and shaft parts machining to ensure machining accuracy and surface quality.
Equipment maintenance and updates: Regularly maintain and upkeep production equipment to ensure that it is in good operating condition. For equipment with decreased accuracy or aging, timely maintenance or updates should be carried out to ensure the stability of processing quality.
Personnel training and management: Strengthen the skill training of production operators to familiarize them with the production process and quality requirements of K47 reducer, and master the correct operating methods. At the same time, establish a comprehensive personnel performance evaluation system to motivate employees to improve their work quality.
Assembly process control
Parts cleaning and protection: Before assembly, thoroughly clean all parts to remove residual oil stains, iron filings, and other impurities during the processing. Take appropriate protective measures after cleaning to prevent the parts from being contaminated or rusting again.
Assembly accuracy control: Strictly follow the assembly process specifications to control the assembly position, clearance, interference fit and other parameters of each part. Use high-precision assembly tools and measuring instruments, such as vernier calipers, micrometers, dial indicators, etc., to monitor and adjust assembly accuracy in real time.
Assembly environment management: Keep the assembly workshop clean, dry, and at an appropriate temperature to avoid factors such as dust and moisture affecting assembly quality. For some high-precision assembly processes, dedicated clean assembly areas can be set up.
Testing and experimentation process
Intermediate process inspection: During the production process, timely inspection is carried out on the machining quality of key processes, such as the tooth profile and tooth direction accuracy of gears, the dimensional accuracy and positional tolerance of shaft parts, etc. Through methods such as first article inspection, patrol inspection, and finished product inspection, quality issues are promptly identified and corrected to prevent non-conforming products from entering the next process.
Finished product performance testing: Conduct comprehensive performance testing on the assembled K47 reducer, including no-load test, load test, temperature rise test, noise test, etc. Test whether its performance indicators such as transmission efficiency, load-bearing capacity, and stability meet the design requirements.
Non destructive testing: Non destructive testing techniques such as ultrasonic testing, magnetic particle testing, etc. are used to perform non-destructive testing on key components of the gearbox, promptly detecting potential defects such as cracks and sand holes, ensuring the safety and reliability of the product.